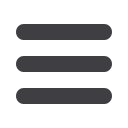
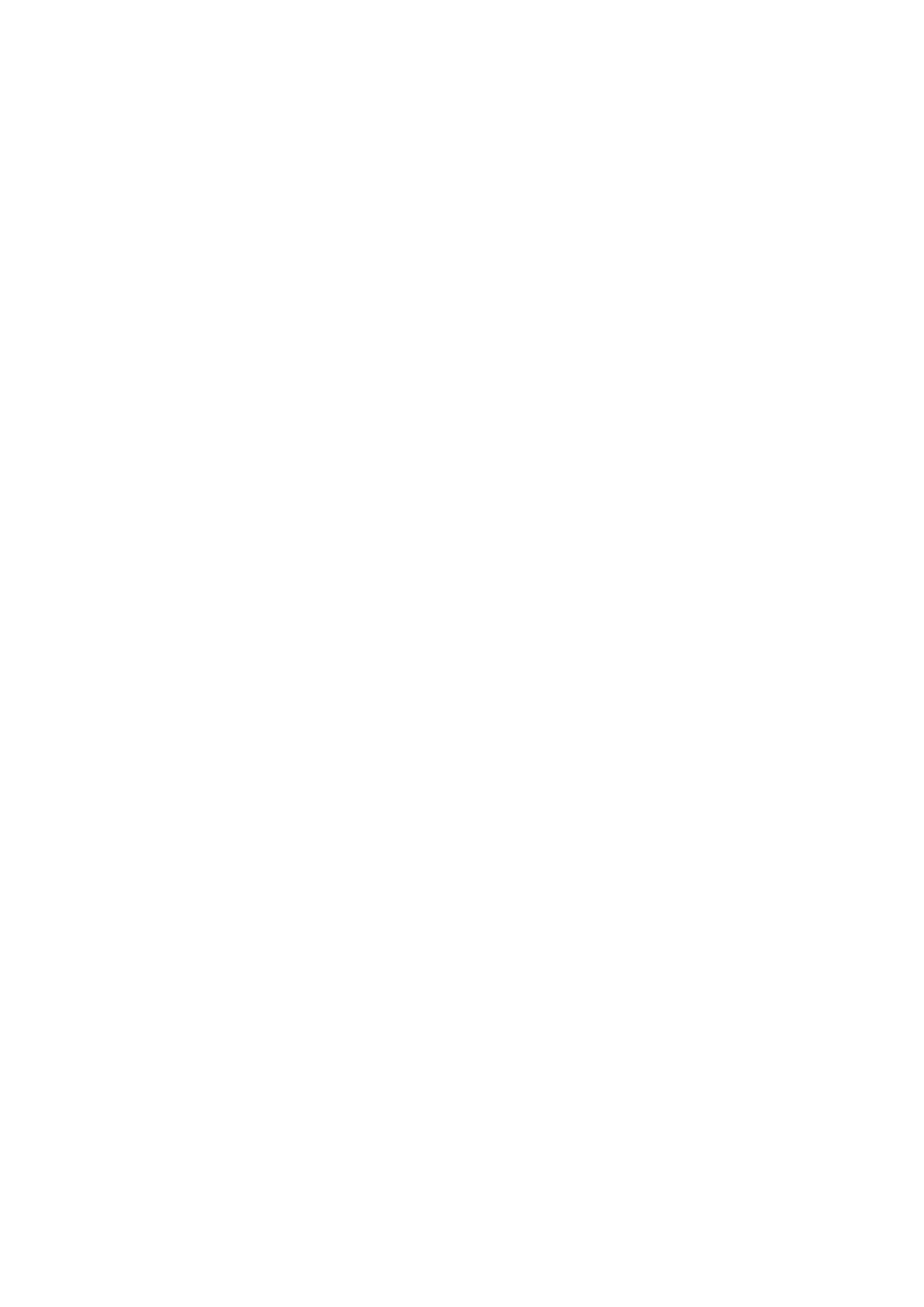
BEAM P
LUS FOR
N
EW
B
UILDINGS
I
NDOOR
E
NVIRONMENTAL
Q
UALITY
(I
EQ
)
V
ERSION
1.2
I
EQ
2 P
LUMBING AND
D
RAINAGE
Copyright © 2012 BEAM Society Limited. All rights reserved.
Page 145
system pressure variations cause air-entrained bubbles to pass
through the water seal; and/or
complete or partial trap seal loss.
Unless water is replenished, from time to time, by the building users or
through discharge of waste water, cross-contamination is likely. Viruses
can enter in indoor spaces through water traps if water seals are dried
out or contaminated, or there is leakage in pipework.
Under working and test conditions traps should retain a minimum seal of
25mm of water or equivalent. Self priming type drainage traps or
drainage pipe connections which ensure trap priming may be
considered, e.g. connection of washbasin discharge to the pipe between
the floor drain grating and its U-trap. Care should also be taken to
prevent back-flowing at the floor drain.
Any provision requiring modification of the relevant Building (Standards
of Sanitary Fitments, Plumbing, Drainage Works and Latrines)
Regulations may be considered by the Building Authority on the merits of
the individual case upon application.
T
WO
-
PIPE
S
YSTEM
According to regulations [2], waste pipes must be connected to a soil
pipe. Use of two pipes for drainage, one for foul water and one for
greywater, may also be a consideration (note that such an arrangement
can allow for greywater recycling). Separation of soil and waste pipes
can reduce the chance of cross contamination between systems. The
connection of wash basin; bath and floor drain to the same waste stack
can still permit cross contamination within the waste system. A more
effective measure is to provide an independent stack for floor drains.
However, the use of a one-pipe system of combined soil and waste stack
has been commonly used in Hong Kong for decades. Many local
designers do not regard the adoption of separate stacks for soil and
waste as a practical and cost-effective solution because it does not
resolve the problem of drying out U-traps. The amount of drainage
pipework will be doubled and, besides extra cost, can impose spatial
constraints [3].
I
NSTALLATIONS
Leaky joints and broken drainage pipes are the result of the lack of
regular inspection and maintenance. Pipework needs to be as accessible
as possible in order to carry out such work, and building management
should be provided with means for regular inspection, maintenance and
repair of building drainage systems.
M
AINTENANCE
A common problem is the difficulty of gaining access to systems from
public or common areas. Locating pipework on the exterior of a building
has the advantage that maintenance can be carried out with minimal
disturbance to users; however, locating pipework internally is acceptable
if adequate duct space is provided with proper access from a public area,
such as a common corridor.
As drainage and other service pipes are often placed in lightwells and re-
entrants, when designing these designers should pay special attention to
access for repair and maintenance [4]. The lowest level of re-entrants
and lightwells housing soil and waste pipes or stacks should be
designated as common areas with access, including access through cat-
ladder where appropriate, to facilitate maintenance and clearance of any
2
Regulation 12. Hong Kong Building (Standards of sanitary Fitments, Plumbing, Drainage Works and Latrines) Regulations.
3
Ma Y Y, Lee HV. Institute of Plumbing Hong Kong. Preventing Infection of Virus from Drainage System. August 2003.
4
Buildings Department. Practice Note for Authorized Persons, Registered Structural Engineers and Registered
Geotechnical Engineers, PNAP No. ADV-14 Facilities for External Inspection and Maintenance of Buildings.
http://www.bd.gov.hk/english/documents/pnap/ADV/ADV014.pdf